ESCP Students Are the Second Place Winners in the Industry 4.0 Challenge with Comau and EURADA
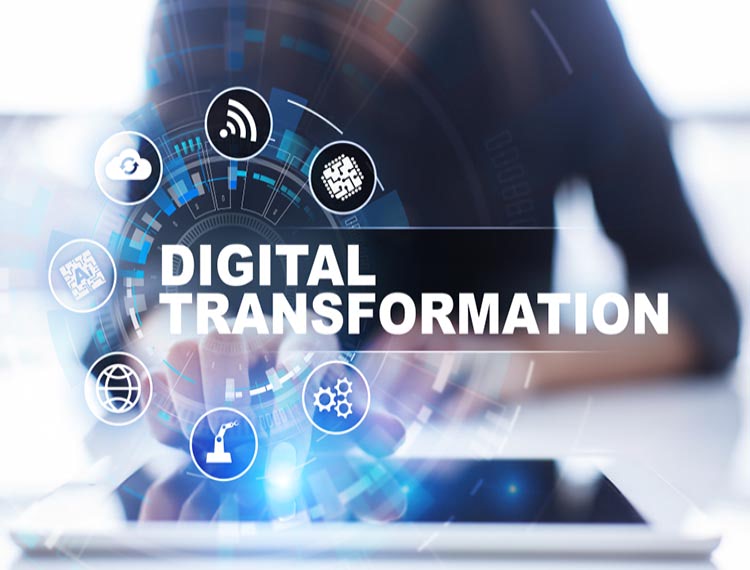
ESCP’s MSc in Digital Transformation Management & Leadership students came second in the Industry 4.0 Challenge with a product that could offer valuable improvements to minimally invasive surgeries, such as laparoscopy, by simplifying the medical procedure, reducing the risks of surgery, and lowering manufacturing costs.
The Challenge, under the topic, ‘Educational robotics as an aid to people for the development of Industry 4.0 skills’, was organised by Comau and EURADA on 25-26 February, as part of the EU Industry Week 2021.
10 teams consisting of industry professionals from leading technology and manufacturing companies across Europe had the opportunity to access the e.DO Cube, a virtual simulator of e.DO Robot, with constant support from the Comau team. e.DO Robot is an educational robotic arm developed by Comau, while e.DO Cube is a product that allows users to program a virtual e.DO Robot, even without the robot itself.
Each team, with their own skills and creativity through e.DO Cube, were challenged to invent, design and propose innovative solutions within the field of Industry 4.0. The results and winners were announced on 12 March 2021. The teams had to design an innovative product, using Additive Manufacturing (3D Printing) and a six-axis robot, to solve a problem related to the United Nations’ Sustainable Development Goals, keeping in mind factors like innovation, feasibility and originality. Teams had to showcase their product to the jury by using a video presentation; program a robot to show the manufacturing process of the product; and finally, submit a document to support the design of the product and its application.
The winning idea
The ESCP Business School team included, Nancy Tohme, Daniel Sze, Carlos Villanueva and Varun Behl, from the MSc in Digital Transformation & Leadership programme and BizTech Society. The students came up with a product based on compliant mechanisms and called it ‘SEAM’ (Surgical instrument designed using the e.Do robot and Additive Manufacturing), to simplify surgery and minimise risk.
Compliant mechanisms could offer valuable improvements to minimally invasive surgeries, such as laparoscopy. The SEAM prototype design aims to merge the three main components needed for the laparoscopy procedure (surgical tools, a high-intensity light, and a high-definition camera) into one single instrument that performs the same functions.
Watch the winning ESCP Team video
What’s next
The ESCP team is now planning a trip to the Comau Headquarters in Turin, Italy, for the “One-day Company Experience” with e.DO Robot and Comau technologies – once the permission to travel abroad has been reinstated.
Comau will be working with the students to identify potential industrial partners to carry out further research on the SEAM product. The team will also participate in the ERASMUS+ Info day at the end of March.
Testimonials
Irene Vetrò, Training Specialist consultant at Comau, reported, ‘The members of the ESCP BizTech team participated in the “Are you ready for Industry 4.0?” Challenge. An event organised within EU Industry Days and promoted by Comau and EURADA (European Association of Development Agencies). Being able to mentor the team during the activity, I noticed, from the beginning, an excellent, natural ability in teamwork, great commitment, and an interest in creating product impact. They focused on building a product of high quality, originality, feasibility and maximum sustainability, reaching a fabulous second position in the challenge. Their product aims to simplify medical procedures by reducing the risks in surgery. A big congratulations to the entire Team! Excellent work!’
Varun Behl, ESCP BizTech team, shared, ‘We came across the Industry 4.0 challenge on LinkedIn and as it aligned with the goals of the BizTech Society at ESCP and the MSc in Digital Transformation Management & Leadership programme, we formed a team of four students who are part of both the society and the programme to register for the event. The other participants were all industry professionals, and we were the only student team to take part. What worked for us was the diversity of our team, which consisted of business school students with previous work experience in architecture, journalism, consultancy and mechatronic engineering – all of us from different countries. Because of these skill sets and our studies at ESCP, we could ace all aspects of the challenge, which included conceiving and designing the product, making a video to pitch our idea, and programming a six-axis robot to simulate how the product will be manufactured. The challenge lasted two full days, was a great learning experience and we enjoyed every bit of working together as a team.’
Responses