Understanding PUWER as a Regulation Ensuring Workplace Safety
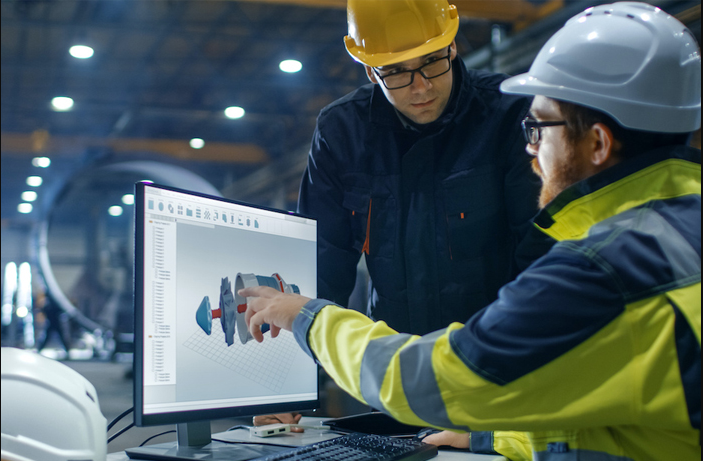
PUWER, also known as Provision and Use of Work Equipment Regulations, is a regulation that requires the safe use of equipment, making sure that it is safe, suitable, maintained, inspected, and installed correctly.
In any workplace, ensuring the safety and well-being of employees should be a top priority. Irrespective of any workplace work, PUWER is a regulation that covers all types of it and aims to ensure the safety of the workers in their industry. Other than that, PUWER also requires the equipment to be used only by qualifies and skilled people, ensuring their safety. PUWER encompasses a wide range of requirements and responsibilities that employers and employees must adhere to, related to use of work equipment in the workplace. In this blog, we will delve into the details regarding PUWER and all the other topics that follow.
PUWER in regards to health and safety
PUWER stands for the Provision and Use of Work Equipment Regulations. The requirements demand that the equipment you use at work is safe and acceptable and that it be properly maintained, inspected, and installed. PUWER also demands that equipment be utilized only by qualified individuals who have received proper knowledge, education, and training.
As PUWER is part of the legislation, therefore it is a legal requirement for workplaces.
What equipment does PUWER cover?
The regulation of PUWER covers every type of work and the equipment used in the operations. From hospitals to warehouses and construction sites, PUWER is a regulation that covers a wide range of work equipment and work tasks. The term “work equipment” in the context of PUWER refers to any machinery, tool, appliance, apparatus, or installation used for work purposes. It includes both fixed and portable equipment. Here are some examples of equipment that PUWER covers:
- Machinery: These include power tools, cutting machines, drilling machines, milling machines, woodworking machinery, metalworking machinery, industrial robots, and other types of machinery used in various industries.
- Vehicles: Vehicles in the workplace, such as forklift trucks, cranes, industrial trucks, construction machinery, etc.
- Lifting equipment: This category includes lifting platforms, hoists, cranes, lifts, and other equipment used for lifting and moving heavy loads.
- Hand tools: Hand-held tools such as hammers, wrenches, screwdrivers, saws, and drills fall under PUWER’s scope.
- Electrical equipment: It includes electrical tools, machinery, appliances, and installations used in the workplace.
- Safety devices and control systems: PUWER covers safety devices such as guards, interlocks, emergency stop systems, and control systems designed to protect employees from potential hazards.
Who does PUWER apply to?
Employers, self-employed people, and anybody who has influence over work equipment are all subject to PUWER. The rules apply to anyone who owns, operates, or uses work equipment. If you buy equipment, rent equipment, or utilize equipment, you should be aware of PUWER.
The usage of equipment covers a broad range of tasks. Even if you are only in charge of shutting off the equipment or cleaning it after it has been used.
The requirement of PUWER
- Risk assessment and control measures: PUWER mandates employers to conduct thorough risk assessments to identify potential hazards associated with work equipment. The employers must then implement control measures to minimize or eliminate these risks. This includes providing suitable protective equipment, ensuring proper maintenance, and implementing safety features.
- Equipment selection and suitability: Under PUWER, employers must ensure that the work equipment used is suitable for the intended task. This involves assessing the equipment’s design, capabilities, and compatibility with the work environment. Factors such as ergonomics and human factors must also be taken into account by the business to prevent repetitive strain injuries and other health issues.
- Inspection, maintenance, and testing: Regular inspection, maintenance, and testing of work equipment are essential to ensure their ongoing safety and performance. Employers must establish maintenance schedules, conduct inspections at appropriate intervals, and arrange for periodic testing and examination by qualified professionals.
- Training and competence: PUWER emphasizes the importance of proper training for employees who work with or operate work equipment. Employers must provide adequate information, instruction, and training to ensure that employees can safely use the equipment. PUWER risk assessment training is crucial in equipping individuals with the skills to assess compliance with PUWER requirements and identify potential hazards by conducting thorough risk assessments in their workplace.
In summary, PUWER requires:
- Equipment to be suitable, maintained, and inspected.
- All employees should be familiar with the instructions and be properly trained.
- Guards and protections should be used to ensure safety with hazardous machinery.
- Employers should select and provide appropriate controls.
- Suitable lighting is provided for safety.
- Equipment should be labelled properly due to health and safety reasons.
- Faulty equipment should be repaired or replaced.
- Employers should ensure that all the work related to mobile work equipment is carried out safely.
- Maintenance operations should be carried out safely.
Responsibilities under PUWER
PUWER places some legal duties on employers and employees in the workplace. Therefore, compliance with the PUWER is a shared responsibility between employers and employees. Below mentioned are the responsibilities of both employers and employees in regard to PUWER.
Employers
- Ensuring equipment is safe and suitable: Employers must provide work equipment that is safe to use, properly maintained, and suitable for the intended tasks. Regular inspections and PUWER risk assessments should be carried out to identify any potential hazards.
- Providing necessary information, instruction, and training: Employers must communicate relevant information, provide clear instructions, and deliver comprehensive training to employees on the safe use of work equipment. This includes highlighting any risks associated with specific tasks and providing guidance on the proper use of safety features.
- Maintenance of equipment and safety measures: Employers must establish maintenance procedures and ensure that regular inspections and servicing are conducted. Additionally, they should implement appropriate safety measures, such as guards, emergency stop systems, and warning signs, to protect employees from potential harm.
Employees
- Following safe working practices: Employees must adhere to the training and instructions provided by their employers. They should use work equipment correctly, follow established safety procedures, and report any defects or hazards they encounter.
- Reporting equipment defects or hazards: If employees notice any equipment defects or hazards, they should promptly report them to their supervisors or the appropriate authority. This helps ensure that necessary action is taken to address the issue and prevent accidents or injuries.
- Cooperating with employers and adhering to training requirements: Employees should actively cooperate with their employers in implementing safety measures and participating in PUWER training programs. Compliance with training requirements is vital to ensure a safe working environment.
PUWER: Health and Safety in the workplace
PUWER regulations serve as a cornerstone for ensuring safety in the workplace, actively safeguarding employees and minimizing potential hazards. By implementing PUWER requirements, employers create an environment where work equipment is meticulously evaluated, controlled, and maintained to mitigate risks. Active adherence to PUWER regulations ensures that machinery, tools, and appliances are carefully selected, compatible with the work environment, and ergonomically designed to reduce the likelihood of accidents and injuries. Thorough risk assessments, performed regularly, enable proactive identification of potential hazards, while the implementation of robust control measures keeps employees protected. PUWER demands that employers invest in comprehensive training programs to teach workers with the knowledge and competence necessary to operate and interact with work equipment safely. Regular inspections and diligent maintenance become second nature, guaranteeing that equipment remains in optimal condition. As a result, PUWER empowers both employers and employees to actively prioritize safety actively, fostering a workplace culture where every individual understands their responsibilities and actively contributes to a secure working environment. Embracing the principles of PUWER is not just a regulatory obligation but a pathway to creating a thriving workplace where safety takes centre stage.
Conclusion
Understanding and complying with PUWER regulations is vital for maintaining a safe working environment. By adhering to the requirements outlined in PUWER, employers can protect their employees from accidents, injuries, and potential legal repercussions. Investing in PUWER assessor training enables individuals to assess compliance, identify hazards, and contribute to a safer workplace. Remember, workplace safety is a collective responsibility, and by prioritizing PUWER compliance, we can foster a culture of safety and well-being for all.
Responses