Tackling skills shortages in the construction industry with UK apprenticeships
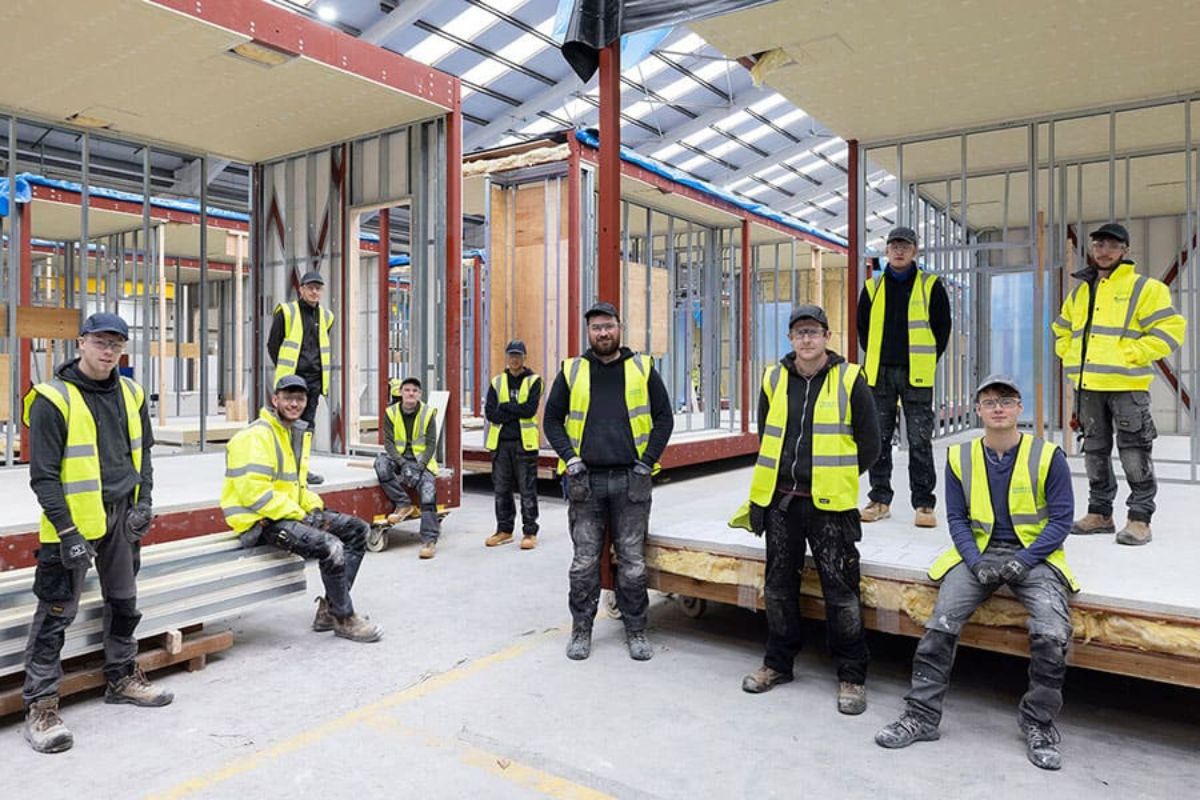
This article discusses how apprenticeships can help solve the skills gap in the manufacturing and construction industry, as well as the importance of flexible learning and training to develop the skills and roles of apprentices. Premier Modular provides case studies of apprentices who’ve risen through the ranks to managerial positions.
Due to the continuous high costs and skills shortages faced by the construction industry, it’s more crucial than ever to hire new personnel and keep hold of existing employees.
As the number of construction employees in the UK declines, especially amongst the younger generation, businesses must quickly address the widening skills gap to meet industry expectations.
The need for construction in the UK is expected to increase by 225,000 employees by 2027, therefore, training the workforce for future expansion is essential to meeting net zero expectations.
How can young people kickstart their careers?
Many young people believe that career development is lacking in the construction business – it’s the responsibility of employers to eliminate this widespread misconception.
The number of apprenticeships in the UK is rising, and attitudes are changing. Apprenticeships offer young people the chance to gain useful skills while earning money, and these courses are recognised as a valid substitute for university education. Apprentices can put their learning into practice by working alongside experienced employees, starting to offer value to their chosen organisation right away.
Rising through the ranks
Lee Cook-Walton, head of rental operations, Premier Modular, explains how his apprenticeship has provided him with a wealth of opportunities.
“I started my career at Premier as a woodworking apprentice for 3 years, followed by a further 3-year apprenticeship in site carpentry and joinery.”
“I grew into a factory supervisor role a few years later, then progressed into a production manager – overseeing all rental division manufacturing elements of the business.”
“My next step was a manufacturing manager, overseeing everything that went through the sales and rental division production units. This involved around 5 factories, consisting of 120 operatives producing 80 modules per week.”
Just over a year ago, Lee decided to move his expertise into rental modular space, becoming the head of UK and European operations.
After being asked why he’s decided to stay at Premier for so long, Lee explained,
“You really do feel like part of a family – the ethos, company values and autonomy of the business are unmatched – we’re trusted to do our jobs but know there’s support when needed. Everyone wants to support each other, and we all have the same vision in mind.”
Since completing his apprenticeship, Lee has continued his education and obtained a variety of professional and personal credentials – including the BDLP (Business Development Leadership Programme), Construction and Business HND (Higher National Diploma), and most recently, Chartered Institute of Building (CIOB) status.
During training, Lee describes the importance of flexible learning:
“To fully develop my skills, I had day releases from work to study. Premier covered these for me – this way I avoided the need to learn in my own time on top of my day job.”
“From day one, Premier has invested heavily in me, and more importantly has put faith in me even when things haven’t gone to plan.”
Mentoring is also available when needed: “Training has been progressive as my roles have changed – I’ve needed to expand my knowledge to adapt to different areas of the business and support my development.”
Versatile experience
Chris Christian, the estimating manager at Premier Modular, began his career as a joinery apprentice before switching to a manufacturing position.
After 3 years of learning on the job, Chris decided a hands-on role wasn’t suited to him: “I moved into a junior estimating role for 3 years, which then progressed into a senior position, allowing me to gain the knowledge needed.”
Since 2022, Chris has worked as an estimating manager within the permanent side of the business. Explaining why he decided to take an apprenticeship, Chris says,
“Apprenticeships are always a good career start – you gain real life experience and build your technical skills. It’s something I’d recommend at a young age – you can always do the traditional university route later down the road.”
“Throughout my time here, the business has supported my progression, continually providing opportunities to grow. I don’t see myself leaving any time soon.”
Flexible training
Sam Sutcliffe, an HR executive with Premier Modular, oversees the onboarding and education of apprentices and serves as the primary point of contact between regional colleges and Premier’s apprenticeship programme.
Describing the importance of filling the skills gap, Sam explains,
“It’s essential we provide training for modular construction and offer involvement within different production departments, for overall business experience.
“As we adapt training around the industry skills needed, we create all-rounders, providing our apprentices with the knowledge required for long-term development within the business.”
“Our future apprenticeship plans include targeting female and BME (Black and Minority Ethnic) candidates, ensuring Premier becomes an even more inclusive career option for everyone.”
Futureproofing
Businesses can make sure they’re turning their workers into adaptable employees by investing in apprenticeship programmes. In order to advance and retain employees, firms must close the manufacturing skills gap – which will support current and future corporate objectives.
By Lee Cook-Walton, head of rental operations, Chris Christian, estimating manager and Sam Sutcliffe, HR executive, Premier Modular.
Responses