Technical dyer and colourist
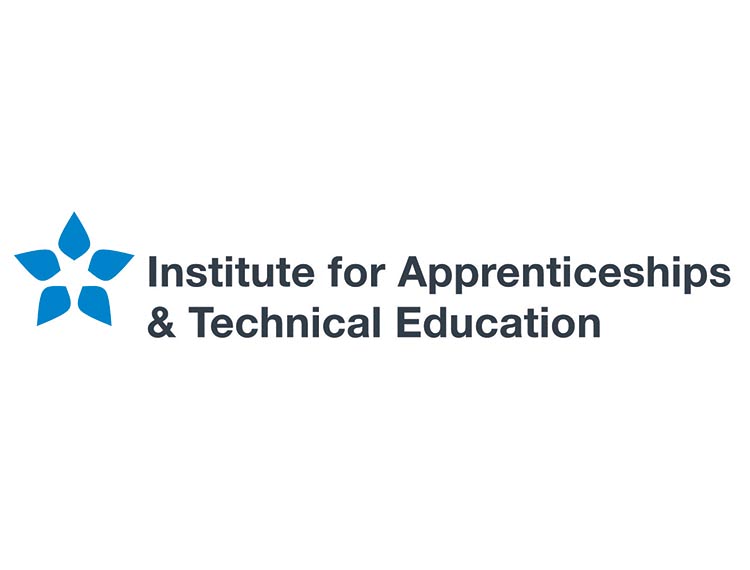
Reference Number: ST0678
Details of standard
Occupation summary
The Technical Dyer and Colourist occupation is found within the textile manufacturing sector. The broad purpose of the occupation is to produce highly specialised dyes and colours to provide dye and colour chemistry in the production of textiles, apparel, upholstery and fashion fabrics.
In their daily work, an employee in this occupation interacts with a wide variety of individuals from the most senior technologists, leaders and directors, to shop floor operatives. Technical Dyers and Colourists work in a factory environment, interchanging between manufacturing facilities and laboratories. Almost all their work is indoors and within a controlled environments where they deal with customers by telephone or email over technical data/job sheets.
An employee in this occupation is responsible for the exact scientific analysis, accurate measurements, trials, production and quality of dyed, pigmented and colour applications to clothing in a heavily industrialised/mechanised scenario. They work in a senior role and lead a team of dyehouse operatives. They report directly to senior management and directors and have overall scrutiny and responsibility for the accuracy of manufactured products within the dyeing and colouration environment. Technical Dyers and Colourists are employed across micro businesses, SMEs and large businesses, ranging from small dyehouse businesses to large chemical, clothing and retail brand businesses.
Typical job titles
Typical job titles include:
Dye-house Technician
Colour Scientist
Colour Chemist
Dye Technologist
Senior Dye-house Supervisor
Laboratory Technician
Laboratory Manager
Manufacturing Managers
Occupation duties
Duty |
Criteria for measuring performance |
KSBs |
Duty 1 undertake production planning and scheduling of dyeing machines. |
– Processing speeds and maintenance logs – Accuracy in production quality; – Standard Operating Procedures; – Compliance with Health & Safety at Work Act; – Adhere to specialist regulations that affect textile manufacturing. |
K1, K2, K3, K4, K5, K6, K7, K8 S1, S2, S4 B2, B3, B4, B5 |
Duty 2 generate dyestuff recipes for shade colour and dyeing containing dyes and auxiliary chemicals. |
– Comply with industry guidelines for chemical and dye usage; – Comply with colour matching expectations; – Comply with shade variations in compliance with industry tolerances; – Manufacture products in line with the Health & Safety At Work Act and REACH regulations; – Delivery service that meets customer expectation and communicate clearly with clients; – Store chemicals and dyes in line with legal practice. |
K9, K10, K11 S1, S6, S7, S8 B1, B2, B3, B4 |
Duty 3 programme and monitor computer controlled dye vessels equipment using control systems to ensure dye colouration cycles run to optimum conditions. |
– Machinery efficiency and production capacity; – Speed, accuracy, temperature, chemical/dye ratio compliant; – Chemical integration with raw materials delivered in line with industry standard (fibre, yarn and fabrics). |
K3, K4, K12, K13, K14 S1, S6, S7, S9 B2, B3, B5 |
Duty 4 managing the dye-house production team. |
– Instruct and communicate clearly with the production team; – Cost jobs and produce proposals with the senior team; – Comply with legal standards for production quality, treatments and properties (i.e. fire proofing/stain resistance); – Advise team on progression and professional development. |
K3, K6, K13 S1, S9, S10, S11 B2, B4, B6 |
Duty 5 control stock and ordering of dyes and chemicals to maximise efficiency and production forecasting. |
– Stock is accurately managed (chemicals and dyes); – Accurate procurement of dyes and chemicals; – Efficient production from data and job sheets; – Comply with import duty tax or tariffs placed upon overseas materials. |
K6, K14 S3, S4, S10 B2, B3 |
Duty 6 produce dye and colour recipes (including recipe adjustments) for batch processing, ensuring that environmental controls for chemicals usage are managed and maintained. |
– Comply with dye production; – Delivery high quality production; – Ensure production compliance for speed and accuracy. – Maximise efficiencies in chemical/dye usage. |
K3, K4 S1, S5, S6, S13 B2, B4, B7 |
Duty 7 undertake client liaison for production planning and delivery to meet client expectations. |
– Adhere to client timescale expectations; – Communicate clearly and succinctly with clients; – Improve service by reporting client feedback. |
K1, K6, K3 S3, S9, S10 B1, B2, B3, B5, B6 |
Duty 8 carry out colour fastness tests and control the quality of finished products before issuing final authorisations for dyeing and colouring of materials |
– Adhere to, and comply with, standard industry testing regulations (tolerance, shrinkage, durability, wash cycle processes) – Deliver customer excellence through test reporting and professional publication of results. – Ensure accurate laboratory testing results in line with standard practice. – Control efficient production. |
K3, K5, K7, K8, K9, K11, K12 S1, S5, S6, S12, S8 B1, B2, B3, B4, B5, B7 |
Duty 9 undertake colour matching in the laboratory including chemical and physical testing of fibres, yarns and fabrics. |
– Comply with accepted industry practice for laboratory testing; – Provide speedy service to clients for undertaking tests and submitting results; – Communicate material needs with customers (fibres, yarns, fabrics). |
K3, K5, K7, K8, K10, K12 S1, S5, S6, S7, S8 B1, B2, B6, B7 |
Duty 10 use bespoke computer software to ensure product specification and consistent testing, analysis and results reporting. |
– Bespoke software efficiently used within company parameters – ICT equipment performs in line with accepted practice; – Deliver in line with customer expectations |
K3, K10, K15 S2, S4, S14, S15 B1, B2, B3, B4, B5, B6, B7 |
Duty 11 control the quality of sample and bulk production in line with industry specifications. |
– Comply with quality checks for consistent production; – Adhere to improvement planning and maintenance scheduling; – Comply with British Standards (ISO); – Communicate changes clearly, within the team. |
K3, K7, K12, K14 S2, S5, S12 B1, B5, B6, B7
|
KSBs
Knowledge
K1: Dyeing and colouration of textiles/fabrics in the overall textile supply chain including the history of dyeing in the UK, the dyeing techniques have evolved and the common practices of dyehouse operations.
K2: Strategies for manufacturing including global resourcing, strategic planning, management culture and expectation and plant operations that effect the manufacturing process.
K3: Product requirements used in dyeing and colouration of yarns and fabrics including production application, variety of use, innovation, cost control and pricing fluctuation.
K4: Risk assessment & management, hazard identification & rectification, safe working systems and an understanding of the legal frameworks that affect textile production, such as Control of Substances Hazardous to Health Regulations, (CoSHH), Registration, Evaluation, Authorisation and Restriction of Chemicals Regulation (REACH) and any other statutory regulations.
K5: Fibre processes, fibre types and specific dyes for coloration manufacturing and how fibres react under chemical processes.
K6: Background and nature of the global textile industry, including how the textile colouration markets are served worldwide, the goods that are procured, the services to business, customer expectations and who the supply chain works.
K7: Hazard protocols including safe storage of dyestuffs and chemicals.
K8: Dye and colour production equipment used for dyeing and colouring fibres, yarns and fabrics for processing.
K9: Colour chemistry in the manufacturing process and how it affects the finished product. This includes the technical knowledge of protein fibres, cellulosic fibres, synthetic fibres, and man-made fibres and the structures of dye molecules.
K10: Chemical and physical theories that underpin textiles from raw material through to finished coloured fabric/garment including colour physics, colour measurement and the implementation in a laboratory and production setting.
K11: Process of applying chemistry to textile colouration including reactions, pH control, methodology and rationale including which fibre with which dye you would select for usage.
K12: Quality and environmental standards appropriate for colour fastness both legislated and advisory in relation to effluent, safe chemical usage, organic textiles and other materials.
K13: Machinery and engineering design, the flow and process of production, dye pressure, suitability, and product preparation used within dye/colour machinery and the effect of processing on product quality.
K14: Environmental controls and implications of failure.
K15: A range of industry ICT systems to determine the correct dye colour
Skills
S1: Create and monitor dye profiles for batch production and batch reporting, ensuring that appropriate decision making to tackle fault or quality issues is effectively undertaken.
S2: Develop operational plans that affect dye manufacturing, including the completion of specialist, technical reports and data to articulate results.
S3: Perform effectively within a team environment and build strong positive working relationships with internal and external customers, colleagues, stakeholders and suppliers to ensure the mission and the ethos of the company is maintained.
S4: Identify and formulate problem solving technical problems associated with errors or critical failures within the coloration industry.
S5: Carry out technical dye profiling for batch production, batch reporting analytics and problem solving/decision making to tackle fault or quality issues.
S6: Use pressure (jet) and atmospheric dyeing techniques and machinery to produce dyed fibres, yarns and fabrics including jig/winch, loose stock, vat, hank, yarn and top dyeing variations.
S7: Identify types of dye process needed to ascertain variations and differences of natural and man-made fibres, such as polyesters, wools, cottons and nylons.
S8: Carry out technical steps in the manufacturing selection process to ensure non-routine dye treatments and application techniques are consistent.
S9: Effective team performance, building positive relationships with stakeholders to ensure the mission and the ethos of the company is maintained throughout the customer journey.
S10: Effectively communicate at all levels, detailing dye and colouration information with clarity, logic and accuracy demonstrating a high degree of technical detail to stakeholders.
S11: Maintain atmospheric and pressure dyeing systems, ensuring that presses, hoists and dispensary equipment including effluent control are managed and maintained, machinery utilisation is maximised and downtime minimised through effective maintenance.
S12: Contribute to operational plans including specialist, technical reports and data to reinforce results and decision making such as Identifying priorities that affect the running of production.
S13: Scrutinise the impact of environment science on dyeing and colouration processes and manage treatments that impact on the environment (such as spillage, effluent leakage, process controlling, implication and remedial activity).
S14: Analyse information, formulate judgements and articulate reasoned arguments through reflection, review and evaluation.
S15: Use relevant ICT systems and machinery such as flow control, valve pressure, valve opening machines and spectrometers to determine the correct dye colour
Behaviours
B1: Acts with honesty and integrity as key indicators of competence whilst promoting a collective ownership of performance through a ‘zero error/right first time’ approach.
B2: Flexibility and adaptability in the workplace, showing positivity in dealing with changing patterns to meet business priorities.
B3: Responsible approach to manage, mitigate and avoid risk through self-awareness, openness and sensitivity to diversity in terms of function, people, culture, business and management activity.
B4: Show energy and enthusiasm in the role including dealing with setbacks, coping under pressure.
B5: Self-manage work constraints in terms of resource, planning, behaviour, motivation and enterprise.
B6: Ensure that client confidentiality is honoured and maintained consistently.
B7: Logical thinker, using cognitive skills to analyse information and identify solutions.
Qualifications
English and Maths qualifications
Apprentices without level 2 English and maths will need to achieve this level prior to taking the End-Point Assessment. For those with an education, health and care plan or a legacy statement, the apprenticeship’s English and maths minimum requirement is Entry Level 3. A British Sign Language (BSL) qualification is an alternative to the English qualification for those whose primary language is BSL.
Professional recognition
TEXTILE INSTITITE / LICENTIATESHIP
Additional details
Occupational Level: 4
Duration (months): 36
Review
This standard will be reviewed after three years.
Crown copyright © 2019. You may re-use this information (not including logos) free of charge in any format or medium, under the terms of the Open Government Licence. Visit www.nationalarchives.gov.uk/doc/open-government-licence
Responses