Automation is the key to getting over 50s back to work (especially for physically demanding roles)
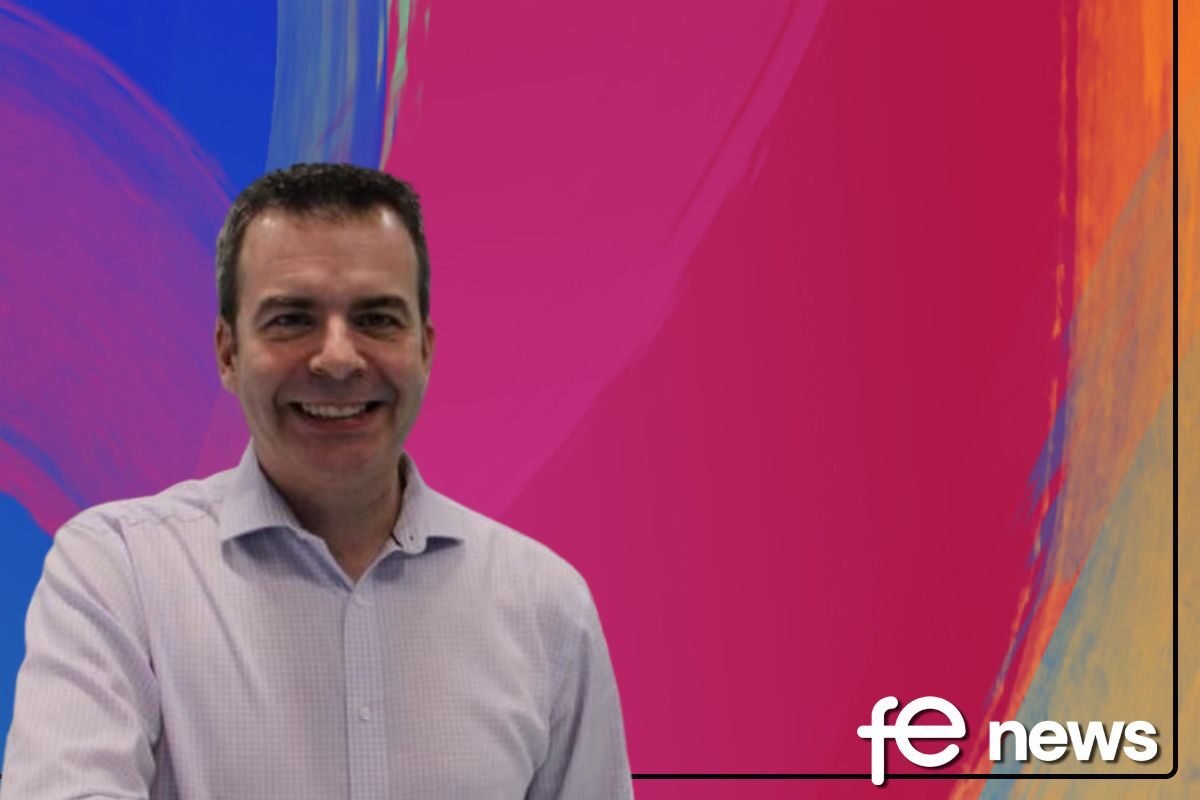
With the UK government encouraging over 50s to return to work to tackle the labour gap, Mark argues that automation will be key to this, particularly in physically demanding roles.
Coined the ‘silver exodus’, an increasing number of over 50s have been steadily leaving the UK workforce due to a lack of career progression and workplace flexibility in recent years. Further exacerbated by the pandemic – ONS data reveals that there are now over 3.5 million over 50s in the UK at pre-retirement age currently not in work.
This is having a detrimental impact across multiple industries but especially when it comes to physically demanding roles, such as those found manufacturing. The physical and tiring nature of the job often means people end up retiring early. This, compounded with fewer young people choosing to enter into the manufacturing sector, is squeezing the workforce at both ends.
This loss of older workers and a failure to attract younger workers has resulted in a shrinking workforce and a skills gap across many UK industries, however, perhaps most impacted is manufacturing. According to PwC’s Annual Manufacturing Report 2020, British manufacturers are facing the largest shortage of workers since 1989 – and things haven’t improved much in the last three years.
It’s vital that we attract both young and old people back into struggling sectors urgently to address the issue, especially as productivity is still yet to return to pre-pandemic levels. We need to give older workers a helping hand by offering them a better work-life balance, instead of what have typically been highly-intensive, laborious jobs based around long shift work.
Robotic automation could be the key to solving the problem. In this article, we will use manufacturing as an example sector to explore how collaborative automation could support wider policy initiatives to encourage this demographic to re-join the workforce.
Unlocking the value of older workers
In the recent UK Budget announcement, the Chancellor called out a focus on encouraging over 50s back to work in order to plug labour shortages across the UK. With measures including raising the cap on tax-free pension contributions and the introduction of ‘returnerships’, it’s clear the government is set on nudging this group back into the workforce.
Similar to apprenticeships, ‘returnerships’ are a new initiative targeted at over 50s returning to work or seeking a career change. They are designed to offer training and support through several dedicated returner programmes that offer people a new pathway into the workforce that makes sense for them.
This is certainly a step in the right direction, but simply offering re-training programmes alone is not enough. Instead, a combination of training and smart technology solutions, such as collaborative robots (cobots), could ease more over 50s back into industries, such as manufacturing.
Removing the barriers to work life balance
It goes without saying that roles in the manufacturing sector are typically manual and exert a lot of physical stress, curtailing the longevity of workers. In fact, this is one reason that many over 50s opt for early retirement and decide to go for less laborious activities. But manufacturing is changing – and the advent of automation is helping make the work less physically intense.
Across multiple industries, automation and cobots can increase output and quality, enable flexible production and improve worker safety. These robots would work alongside people, not replace them, taking on the dull, dirty and dangerous work – allowing workers to focus on tasks better suited to their skills or experience.
Securing future UK productivity
The UK labour shortage will not solve itself and for some sectors, such as manufacturing, it is becoming mission critical. Despite the opportunity presented by automation technology to get over 50s back to work, the UK is currently lagging behind on the global scale, and remains the only G7 nation with a robot density below the global average. Other countries such as Germany and South Korea are miles ahead and see automation as part of their long-term industrial strategy.
While historically, the UK has moved slowly on automation adoption, we need to learn from our G7 neighbours. Automation offers a pathway for both younger workers entering the workforce and older workers looking to re-join. It could be the key to addressing low productivity across the country.
To make this work, policy makers and industry leaders require a better strategy for facilitating collaboration between workers and automation. This means more education and investment. There are a range of options to get over 50s back to work, but automation is one that cannot be overlooked.
By Mark Gray, Country Manager UK & Ireland, Universal Robots
Responses