The three actions we must take to bolster engineering apprenticeships
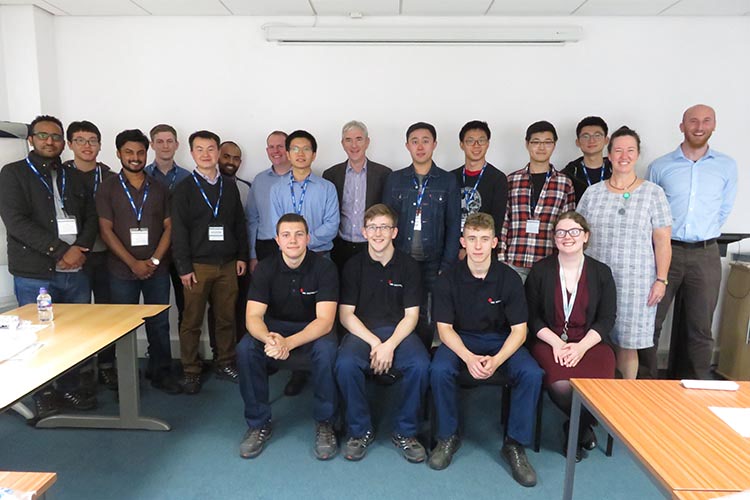
“Skills gap” and “ageing workforce” – two phrases many businesses working in the manufacturing and science industries have become accustomed to hearing.
While we’re confident that we’ve got the right people in our machine shop and manufacturing areas right now, apprentices are an important part of our future.
This means addressing the skills gap by playing an active role in developing the next generation of engineers.
Where we’re based in Trafford Park we’re surrounded by highly-skilled, engineering inclined men and women all across the North West.
Yet due to limited public transport links, recruiting young apprentices can be quite tricky; longer commute times inevitably reduce the recruitment pool making this talent often just slightly out of reach.
In 2017/18 there was a sharp drop in apprenticeships in apprenticeships being undertaken, while universities saw a record level of intake.
In part this is due to the excellent marketing skills of our universities that have done a great job encouraging young people into higher education, however this has been to the detriment of apprenticeships and so the intake of new workers into more traditional trades must have slowed.
Three important things are vital to reverse this trend:
- The next generation needs to be fully educated as to their options at a much earlier age,
- The Levy system should be improved, and
- ‘Myths’ around apprenticeships need to be dispelled
1. Clearer Engineering Options
First, while we acknowledge the university route is a highly credible one and the perfect choice for many, we need to ensure that all school leavers are provided with accurate and timely information regarding all the routes open to them, including apprenticeships, so that they can select the route best suited to achieve their goals.
Further it is not an either/or choice. School leavers and adult learners alike need to know that the possibility of going to university and gaining a degree whilst doing an apprenticeship is also a reality.
To help promote apprenticeships as an attractive option we work proactively with schools and colleges in the local area to help expand the horizons of their students.
We offer site tours and invite parents/guardians to attend during the apprentice interview stage to learn more about working in manufacturing – a real ‘hands on’ experience. We’ve run this scheme for the past two years and, as a result of resounding positive feedback, we intend to continue to do so.
Opening up these channels of communication is an important first step, but changes to the school curriculum would help even more. Introducing the idea of manufacturing at a younger age, exposing children to skills like computer aided design, and wood and metal working would also strengthen the pathway into engineering apprenticeships.
2. Simplify the Levy System
Second, in our experience the foundations of the levy system that supports businesses offering apprenticeships needs to be more user-friendly and, as the system is still being developed, some much-needed manufacturing courses have yet to be supported.
3. Better Promotion of Apprenticeships
Finally, not everything young adults hear about apprenticeships is true. Bad pay? Long days? Endless tea rounds? That couldn’t be further from our truth!
At M&I Materials, we’ve made a conscious decision to pay above minimum wage and pay is linked to achievement.
Our apprentices work 7.30am – 3.30pm, there are no long days here unless they want them!
They’re involved in machining components and learning about different materials from day one.
What’s not to like about getting on-the-job experience, making friends at college and achieving an HNC, while being paid?
Working in engineering is exciting and it can lead down all sorts of interesting roads. An engineering apprenticeship provides both practical knowledge and understanding as well as classroom theory. In fact, it provides a foundation for a lifelong career.
Our apprentices feel a sense of achievement in their work from day 1. They learn about how materials react, adapt and perform in different environments and how to deliver products of the highest quality that are fit for purpose.
From the outset they are valued members of a business that can trace its roots from 1901 to the current day where we proudly deliver excellence for some of the most respected brands in the world from Siemens, Boeing and ABB to Formula 1, Three Gorges Dam and Cern.
There’s obviously something very special in that.
I am proud, very proud of our excellent apprentices and the highly skilled workforce we have here at M&I Materials. People are what makes a successful business and we are no exception.
We will continue to invest in the development of apprentices and encourage and support the flow of curious young minds into engineering, in as many ways as possible.
Having said that, a little more help from government in communicating the true advantages and values of such a career path at a national level would be very warmly received.
Paul Masters, Manufacturing Director, M&I Materials
Responses