Mineral and construction product sampling and testing operations
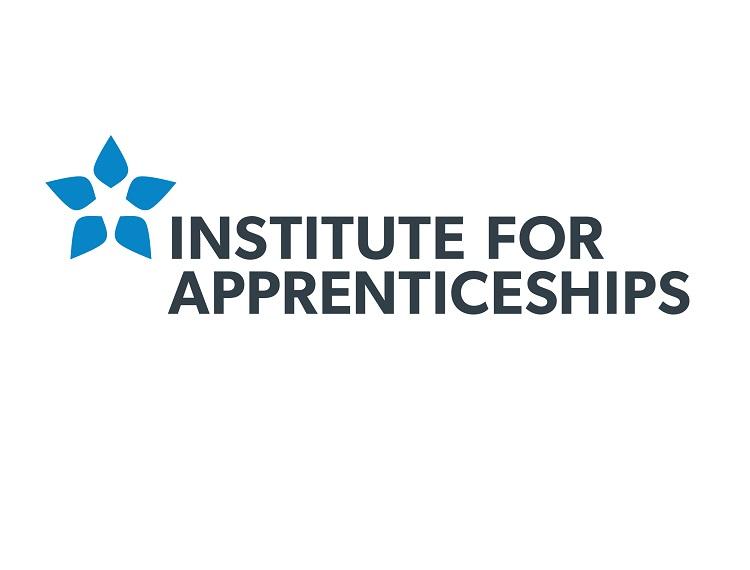
Reference Number: ST0511
Details of standard
Occupational Profile
The Mineral and Construction industries employ around one and a half million people and contribute around £17 billion to the UK economy.
A Mineral and Construction Product Sampling and Testing Operator collects and samples mineral products, heavy construction products and/or final end use products to ensure they meet rigorous British and European standards (BSEN) and to ensure they meet customer specifications. Materials can include ready mixed concrete, cement, mortar, asphalt, road building and high speed rail products, precast and pre-stressed concrete. They work in a range of subsectors including mining, construction, quarrying, road building, waste and recycling operations. As product failure and poor quality can lead to end use failure, expert knowledge and attention to detail is essential.
A Mineral and Construction Product Sampling and Testing Operator can:
- Collect and sample products at source and/or on customer site.
- Report findings verbally and in writing in accordance with BSEN standards.
- Suggest ways to improve quality of products using knowledge of the material and production process.
- Use specialist equipment in order to grade materials, use compression and flexural testing equipment in order to measure strength, use nuclear density, thermocouples for temperature, slump and spread measurement equipment and methods for chemical analysis in order to check product quality, workability and consistency.
- Prepare reports on quality measures and key performance indicators (KPIs).
- Control raw material constituents by ensuring they are safely used and stored.
- Use their knowledge of materials to minimise waste and support recycling.
- Diagnose faults with sampling/testing equipment taking steps to rectify them.
They usually report to the technical site supervisor, but can also work autonomously and have the ability to make decisions. This is a key role supporting the entire production process. Due to the safety critical nature of the role, attention to detail is essential. Working safely and ethically is paramount as the sector is highly regulated so they always demonstrate an excellent understanding of site, regulatory, safety, health and environmental issues.
Entry requirements
Individual employers will set the entry requirements for this apprenticeship.
KNOWLEDGE |
What is required, an understanding of: |
Health and safety |
|
Effective communications |
|
Commitment to code of ethics |
|
Product and technical knowledge |
|
SKILLS |
What is required, an ability to: |
Health, safety & environment |
|
Sampling and testing tasks |
|
Communications |
|
Commitment to code of ethics |
|
I.T. |
|
BEHAVIOURS |
What is required, will: |
Professional judgement |
|
Continuing professional development (CPD) |
|
Customer service |
|
Accepting responsibility |
|
Efficiencies |
|
Duration:
Typically, 14 – 18 months
Qualifications:
MPQC Level 2 Certificate in Laboratory and Associated Technical Activities for Mineral Products Operations must be achieved to meet regulatory requirements within the sector.
Apprentices without level 1 English and Maths will need to achieve this level and take the test for level 2 English and Maths prior to taking the end-point assessment. For those with an education, health and care plan or a legacy statement the apprenticeships English and maths minimum requirement is Entry Level 3 and British Sign Language qualification are an alternative to English qualifications for whom this is their primary language.
Level:
2
Review date:
After three years.
Crown copyright © 2017. You may re-use this information (not including logos) free of charge in any format or medium, under the terms of the Open Government Licence. Visit www.nationalarchives.gov.uk/doc/open-government-licence
Responses